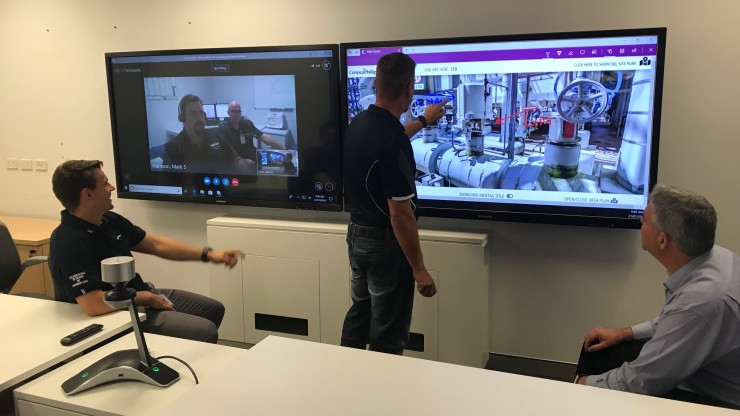
The DLNG team has taken innovation to a new level, trialling 3D visualisation technology ‘Virtual DLNG’ which will revolutionise Perth-Darwin collaboration.
The DLNG team has taken innovation to a new level, trialling 3D visualisation technology ‘Virtual DLNG’ which will revolutionise Perth-Darwin collaboration.
State of the art photographic scanning was recently completed at DLNG creating a google-maps-style simulated walkthrough of the plant. This software will allow designers and engineers to virtually ‘visit’ DLNG at any time, enabling unprecedented facility access.
The idea was born when Reza Dashti, Project Engineer, created a 3D tour for his rental property to help conduct inspections. When sharing this with his colleagues, they commented “we need this for DLNG!” and the idea was born. Innovation can stem from something as simple as a chat between workmates.
Collaboration in action – Perth and Darwin staff using Virtual DLNG
A collaboration room at the Integrated Operations Support Centre in Perth has been set up with a 360 degree camera, allowing multi-site meetings to run as though everyone is in the same room. Virtual DLNG enables immediate access for engineers and designers across locations to view plant equipment in a matter of minutes, improving efficiency in the inspection and decision making process. Furthermore, this creates cost saving benefits, decreases HSE risk to personnel, while optimising site visit requirements.
The software has embedded ‘tagging’ functionality allowing for equipment, scopes of work, engineering documents and even videos to be interactively tagged into the ‘virtual tour.’ Examples include hyperlinks to controlled documents (e.g. SAP), an embedded time-lapse video showing how to safely change out a turbine or filter, or even access to view a past scaffold build.
Virtual DLNG visualisation
Although the 3D visualisation was initially produced for the team working on DLNG backfill, there is limitless potential for innovative process improvements within other functions of the Business Unit. From providing a Perth-based accountant an understanding of the facility they support, to enhancing site inductions for shutdown crews, Virtual DLNG is the future of ABU-West. The Backfill team are also continually looking for more ways to create value with the tool, including using it to create a true One Team project with the Engineering, Procurement and Construction contractors.
Members from the Timor-Leste process team travelled to Perth to help tag the scopes of work within the visualisation. Their assistance will help finalise Virtual DLNG as a tool for internal and external stakeholders to fully understand the scopes and associated physical constraints.
From left to right: Richard Thompson - ViewTech 3D, Jucilia Belo - TL Junior Designer, Reza Dashti – Project Engineer, James Hodge - E&I Operations Specialist, Diamantino Soares - TL Junior Designer